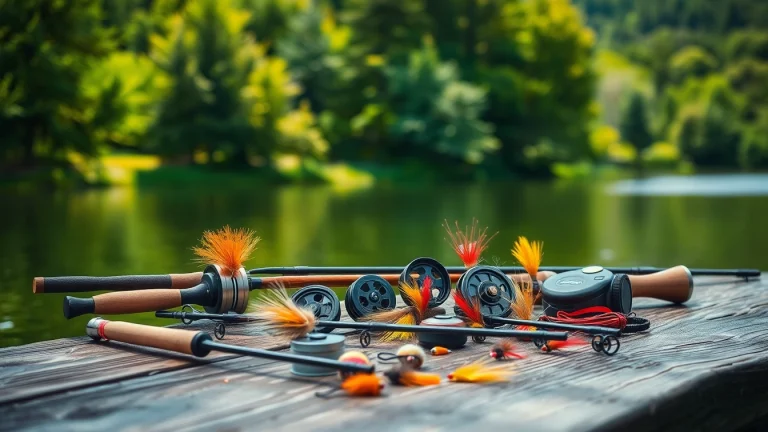
Essential Guide to Choosing the Right Fly Fishing Kit for Your Adventures
Understanding the Basics of a Fly Fishing Kit
Fly fishing is an art that transcends mere fishing. It requires skill, patience, and the right equipment. A beginner venturing into this hobby may find themselves overwhelmed with options and jargon. However, understanding the essentials of a fly fishing kit can simplify the process significantly. In this section, we’ll break down the key components of a fly fishing kit, the material and quality aspects to consider, and the benefits of using a comprehensive kit.
Components of a Fly Fishing Kit
A fly fishing kit typically includes several key components that work together to create an effective fishing experience. Here’s a breakdown of each item:
- Fly Rod: The rod is crucial as it determines casting technique and distance. Most beginner kits feature a medium-weight rod that is versatile for various fishing conditions.
- Fly Reel: The reel is where the line is stored and retrieved. It helps manage the line during casting and when a fish is hooked.
- Fly Line: This specialized line is thicker than regular fishing line, allowing it to float on the water’s surface. It’s essential for casting the fly to desired locations.
- Tippet: A thin line attached to the fly, the tippet helps to make the fly look more natural in the water.
- Flies: Imitating insects or bait fish, flies are used to attract the fish. They come in various patterns and sizes.
- Accessories: This may include tools such as nippers, forceps, and fly boxes to organize and protect flies.
Material and Quality Considerations
When selecting a fly fishing kit, material and quality are paramount. Rods can be made from graphite, fiberglass, or bamboo, each offering different levels of sensitivity and durability. Graphite rods are popular for their lightweight nature and responsiveness, making them ideal for beginners.
The reel’s construction usually features aluminum or plastic; aluminum being more durable and suitable for larger fish. It’s essential to choose high-quality components that ensure longevity and reliability while on the water. Investing in a higher quality fly fishing kit often pays off in terms of performance and enjoyment.
Benefits of Using a Fly Fishing Kit
Using a well-curated fly fishing kit carries numerous advantages:
- Convenience: A complete kit simplifies the process of getting started, as it provides all necessary components in one package.
- Cost-Effectiveness: Purchasing a kit can be more economical than buying components individually, especially for beginners.
- Makes Learning Easier: With everything you need in one kit, newbies can focus on perfecting their technique rather than hunting down gear.
Choosing the Perfect Fly Fishing Kit
Selecting the right fly fishing kit involves thoughtful consideration of various factors. Every angler is different, and understanding your specific needs and budget can guide you in making the best choice. Here’s a closer look at how to identify your fishing needs, budget accordingly, and recognize the essential features of a great kit.
Identifying Your Fishing Needs
Before making any purchase, assess what you intend to achieve with your fly fishing. Consider the following:
- Type of Fishing: Will you be fishing in freshwater or saltwater? Target species can dictate the type of gear needed.
- Your Skill Level: Beginners should opt for user-friendly kits with forgiving equipment, while seasoned anglers may seek specialized gear.
- Local Conditions: Understanding the water conditions in your area can inform your kit choice. For example, fast rivers may require different setups than still ponds.
Budgeting for Your Fly Fishing Kit
Setting a budget is critical when pursuing a fly fishing kit. Consider your commitment to the sport; if you are just starting, it might be wise to invest in an entry-level kit that won’t break the bank. However, if fly fishing becomes a passion, you may want to allocate funds for a higher-end rod and reel. A general guideline is to expect to spend anywhere from a couple of hundred to over a thousand dollars depending on component quality and brand.
Top Features to Look For
The best fly fishing kits share several important features:
- Ease of Use: Kits designed specifically for beginners typically include lightweight rods, straightforward reel systems, and clear instructions.
- Versatility: A quality kit should cater to various fishing locations and species, ensuring that you can grow into the gear as your skills progress.
- Durability: Look for materials resistant to wear and tear, particularly if you plan on fishing in rugged environments.
How to Maintain Your Fly Fishing Kit
Proper maintenance of your fly fishing kit not only ensures longevity but also enhances your overall fishing experience. This section covers best practices for cleaning your gear, storing your kit securely, and knowing when and how to perform repairs.
Cleaning Your Fishing Gear
After every fishing trip, it’s vital to clean your equipment. Here are key steps to follow:
- Rinse Your Rod and Reel: Use fresh water to rinse off any dirt, algae, or salt left from fishing.
- Check Your Lines: Look for frays or weaknesses in your fly line, as these can impede casting and landing fish.
- Store Flies Properly: Ensure that flies are dry before placing them back in storage to prevent rusting of hooks and deterioration of materials.
Proper Storage Techniques
How you store your fly fishing kit matters greatly. Consider these tips:
- Use Protective Cases: Store your rod in a protective tube to prevent damage during transport.
- Keep Your Reel Out of the Sun: Prolonged exposure to UV rays can deteriorate reels, especially plastic ones.
- Maintain Dry Conditions: A cool, dry place is ideal for storing your fly fishing kit to prevent mold and mildew.
Repairing and Replacing Parts
Over time, components of your fly fishing kit may need repair or replacement. Here are some common issues:
- Reel Malfunctions: If your reel is not functioning smoothly, it may require lubrication or a component replacement.
- Rod Damage: Small scratches can be repaired, but breaks in the rod often necessitate a replacement.
- Line Issues: Regularly replace tippet and fly line to maintain optimal performance.
Essential Tips for Beginners with Their Fly Fishing Kit
As a beginner, the learning curve can be steep, yet knowing some foundational tips can significantly enhance your fly fishing experience. This section will outline key casting techniques, best practices for setting up your kit, and the importance of understanding local fishing regulations.
Mastering Basic Casting Techniques
Effective casting is essential for success in fly fishing. Here are a few techniques to master:
- Overhead Cast: The basic casting method, where the rod is raised above your head and the line is cast forward with a flick of the wrist.
- Roll Cast: Ideal for situations with limited back casting space. It uses a smooth forward motion and relies on the line’s weight to push the fly out.
- Sidearm Cast: Great for windy conditions, allowing the angler to keep the fly low and prevent line tangles.
Best Practices for Setting Up Your Kit
Getting your fly fishing kit set up properly is crucial for a successful outing. Here’s how:
- Choose the Right Fly: Tailor your fly choice to the species you aim to catch, and ensure it matches local conditions.
- Attach Tippet Correctly: Tippet should be tied securely to your leader for an efficient connection to your fly.
- Practice Casting: Before hitting the water, practice casting in an open space to improve your technique.
Understanding Local Fishing Regulations
Being aware of local fishing laws is imperative for responsible angling. Every region has specific regulations regarding:
- Permits: Some areas require licenses or special permits; check local guidelines.
- Catch Limits: Knowing what species you can keep and their limits ensures sustainable fishing practices.
- Seasons: Some waterways have open and closed seasons for different types of fish.
Advanced Techniques for Experienced Fishermen Using Fly Fishing Kits
For seasoned anglers, mastering advanced techniques can elevate the fly fishing experience. This section will delve into experimenting with fly patterns, utilizing technology, and engaging with the fly fishing community for continued growth.
Experimenting with Fly Patterns
Experienced anglers often develop a collection of flies and frequently experiment with different patterns for various conditions:
- Dry Flies: Used to imitate insects floating on the water surface, they are perfect when fish are actively feeding on surface bugs.
- Wet Flies: These sink just below the surface and mimic insects emerging from larvae.
- Nymphs: Practical at different depths for catching fish feeding just below the surface.
Utilizing Technology in Fly Fishing
Technology has transformed fly fishing, making it easier for anglers to enhance their skills and improve their success rate:
- Apps: Numerous applications provide weather updates, fishing reports, and local hotspots.
- Smart Reels: New technology can monitor line tension and help enhance your retrieval techniques.
- Online Communities: Engaging through social media and forums can lead to invaluable tips and shared experiences.
Engaging with the Fly Fishing Community
Being part of the fly fishing community can significantly enrich your fishing journey. Here’s how to engage:
- Local Clubs: Joining clubs offers networking opportunities and access to group outings.
- Workshops and Seminars: Attending classes can hone your skills and introduce you to new techniques.
- Contributing to Conservation: Engaging with initiatives aimed at protecting aquatic habitats fosters sustainable practices for future anglers.