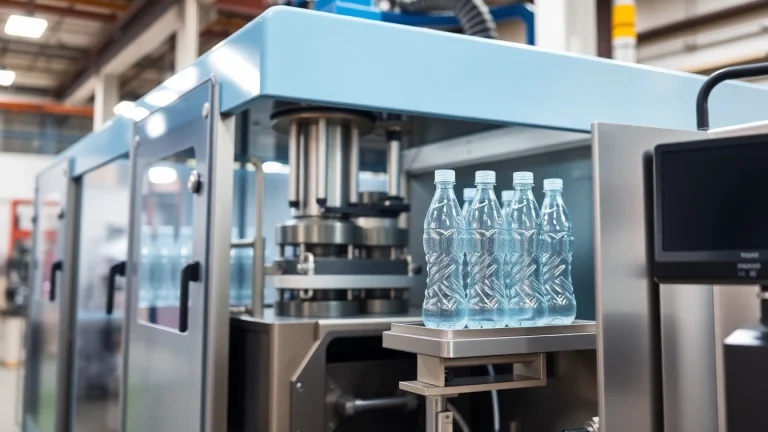
Leading Blow Molding Machine Manufacturer for Efficient Production Solutions
Introduction to Blow Molding Technology
Blow molding is a transformative and crucial method in the manufacturing sector, particularly for creating hollow plastic objects like bottles and containers. This sophisticated technique harnesses the unique properties of thermoplastics, allowing manufacturers to produce versatile and durable products rapidly. As industries worldwide seek efficient production solutions, the role of a quality Blow Molding Machine Manufacturer becomes increasingly significant.
What is Blow Molding?
Blow molding is a manufacturing process that involves inflating heated plastic into a mold to form a specific shape. The procedure typically starts with thermoplastic resin, which is melted and extruded into a parison—a hollow tube of plastic. This parison is then placed in a mold, where air is blown into it, causing the plastic to expand and take on the mold’s shape. This method is widely used for creating containers, panels, and other items where hollow shapes are needed.
Types of Blow Molding Processes
There are primarily three types of blow molding processes: Extrusion Blow Molding (EBM), Injection Blow Molding (IBM), and Stretch Blow Molding (SBM). Each method has its unique advantages and suited applications.
- Extrusion Blow Molding (EBM): This process is commonly used for producing larger containers, such as bottles and tanks. The parison is extruded and then inflated into a mold. It is an efficient method for high-volume production.
- Injection Blow Molding (IBM): Suitable for small and intricate products, this method involves injecting the molten resin into a core for shaping before it is blown into the final mold, ensuring high precision and detail.
- Stretch Blow Molding (SBM): Primarily employed for PET bottles, this method stretches the parison to enhance clarity and strength. It is especially popular in the beverage industry for its ability to produce lightweight yet durable packaging.
Applications of Blow Molding
Blow molding is prevalent in various industries, particularly in manufacturing packaging solutions, automotive components, and consumer goods. Here are some applications:
- Packaging: The most common application, including bottles, jars, and containers for food, beverages, and cosmetics.
- Automotive: Manufacturing lightweight and durable parts such as fuel tanks and bumpers.
- Industrial: Producing larger containers and tanks for chemicals and other fluids.
Choosing the Right Blow Molding Machine
Selecting the right blow molding machine is critical for businesses looking to optimize production processes. Various factors come into play that can influence the efficiency and output of the manufacturing setup.
Factors to Consider
When choosing a blow molding machine, consider these essential factors:
- Type of Blow Molding: Depending on the final product, select between EBM, IBM, or SBM techniques.
- Production Volume: Assess your production needs to determine if a high-speed machine or a more flexible option is best.
- Mold Compatibility: Ensure that the machine can accommodate existing molds or if new ones will be needed.
- Automation Level: Automated machines can reduce labor costs and increase precision and repeatability.
Cost vs. Quality Analysis
Investing in blow molding machinery requires a careful analysis of cost versus quality. High-quality machines often provide better reliability, efficiency, and output. While the initial investment might be higher, the long-term savings from reduced maintenance and improved production can be substantial. It is essential to conduct a thorough total cost of ownership (TCO) analysis to align with organizational budgets and production goals.
Customization Options
Customization is often a key differentiator among blow molding machine manufacturers. High-quality manufacturers provide a range of options to suit specific production needs, including:
- Custom Molds: Design molds tailored to your unique product specifications.
- Machine Configuration: Adapt machine layouts and functions based on production line requirements.
- Integration with Existing Systems: Options for seamless integration with pre-existing manufacturing technologies.
Top Blow Molding Machine Manufacturers
When it comes to blow molding, selecting the right manufacturer is crucial. Here’s an overview of some industry leaders and their offerings:
Industry Leaders Overview
Prominent names in the blow molding machine sector include:
- Uniloy: A recognized leader offering four unique blow molding technologies, including both molds and tooling.
- Wilmington Machinery: Known for high-speed, monolayer, and multilayer rotary extrusion blow molding machines.
- Jomar Corporation: Celebrated for its injection blow molding machines, delivering precision and quality over five decades.
- Bekum Maschinenfabrik: Offers a successful H-series of blow-molding machines, well-regarded throughout America.
Comparative Analysis of Features
Conducting a comparative analysis helps identify the right machine based on the following features:
- Speed: Machines vary in speed; the selection depends on production demands.
- Precision and Tolerances: Assess machine capabilities for the precision required in your products.
- Ease of Operation: User-friendly interfaces can significantly reduce training time and operational challenges.
Customer Testimonials
Understanding customer experiences can provide insight into the reliability and performance of different machines. Satisfied customers often report improved efficiency and product quality by working with reputable manufacturers. For instance, many of Jomar’s clients praise their machines for the exceptional quality of the end products and the substantial decrease in defect rates.
Maintenance and Support for Blow Molding Machines
To guarantee ongoing productivity, proper maintenance and support for blow molding machines are crucial. This section explains best practices and troubleshooting techniques to ensure machines operate smoothly.
Routine Maintenance Guidelines
Regular maintenance ensures longevity and efficiency. Key maintenance guidelines include:
- Perform daily checks on machine components, including heating elements, mold condition, and air pressure levels.
- Schedule regular cleaning sessions to prevent contamination from leftover plastic residue.
- Maintain a log of machine performance to identify trends or emerging issues before they escalate.
Common Issues and Solutions
Operators may encounter various issues while using blow molding machines. Here are common problems and their solutions:
- Defects in Products: Often due to inadequate cooling or incorrect mold setup. Ensure proper heating and cooling cycles are followed.
- Inconsistent Wall Thickness: This can arise from improper air pressure or inconsistent extrusion speed. Adjust parameters accordingly to stabilize output.
- Machine Downtime: Regular maintenance and prediction of potential failures can dramatically reduce unexpected breakdowns.
Availability of Spare Parts
For manufacturers, ensuring the availability of spare parts is essential for minimizing downtime. Selecting a manufacturer who provides comprehensive spare parts inventory is vital. This leads to quicker repairs and maintains production schedules. A robust support system can significantly impact operational efficiency.
Future Trends in Blow Molding Technology
As technology advances, so too does blow molding. Staying abreast of emerging trends is crucial for remaining competitive in this evolving market.
Innovations in Eco-Friendly Materials
As sustainability becomes a central concern for many industries, the development of eco-friendly materials has taken the forefront in blow molding technology. Biodegradable plastics and recycled materials are paving the way for more ethical production practices. Manufacturers are increasingly investing in research to integrate these materials into existing production lines without sacrificing product quality.
Automation and Industry 4.0
The advent of Industry 4.0 is revolutionizing production processes, including blow molding. Technologies such as IoT and machine learning are being integrated into blow molding equipment for enhanced performance monitoring and optimized operations. Automated systems can lead to less human error, increased production rates, and better data collection for ongoing improvement initiatives.
Market Growth Predictions
The blow molding industry is expected to witness robust growth in the coming years, driven by rising demand in sectors such as packaging and automotive. Market analysts predict an increase in the global blow molding machine market, fueled by advancements in technology and increasing manufacturing capacities in emerging economies.