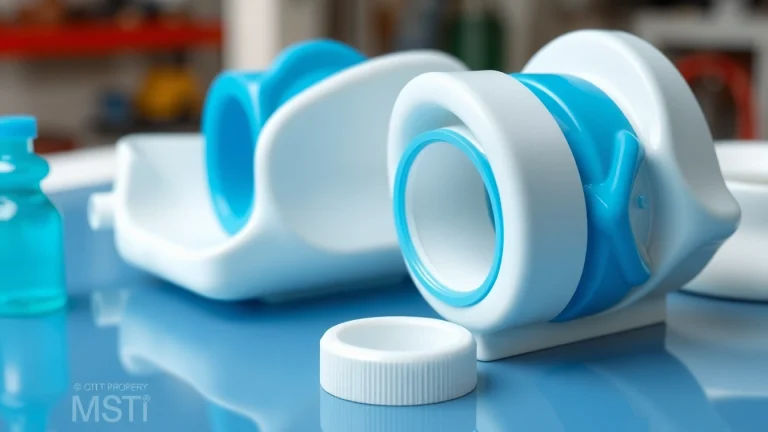
Top Blow Molding Machine Manufacturer for High-Efficiency Production Solutions
Understanding Blow Molding Technology
In the world of manufacturing, blow molding technology plays a pivotal role in creating a variety of hollow plastic products. As a Blow Molding Machine Manufacturer, it is essential to understand the fundamentals of this technique, its processes, and applications. By delving deep into this technology, businesses can make informed decisions that enhance their production efficiency and product quality.
What is Blow Molding?
Blow molding is a manufacturing process used to create hollow plastic parts by inflating a heated plastic tube, known as a parison, inside a mold. The process can be broken down into several stages, involving the melting of plastic resin, forming the parison, and then shaping it into the desired hollow structure. This technique is significant for producing items like bottles, containers, and other hollow shapes, making it a cornerstone for industries ranging from consumer goods to pharmaceuticals.
Types of Blow Molding Processes
There are three primary types of blow molding processes utilized by manufacturers:
- Extrusion Blow Molding (EBM): This is the most common method, where molten plastic is extruded into a parison shape, and then air is blown into it while it is in the mold to form hollow objects.
- Injection Blow Molding (IBM): In this process, plastic is first injected into a mold to create a preform. The preform is then transferred to a blow mold where air is introduced to form the final shape.
- Stretch Blow Molding (SBM): Primarily used for manufacturing PET bottles, SBM involves stretching the plastic (preform) while it is molded, resulting in a stronger product.
Applications of Blow Molding
Blow molding technology is versatile and is widely used across various industries. Key applications include:
- Packaging: The most common application, producing bottles for beverages, detergents, and personal care products.
- Automotive: Creating components such as fuel tanks and interior trim parts.
- Toys: Manufacturing hollow toys that are lightweight and safe for children.
- Industrial Containers: Large storage containers used for chemicals, food products, etc.
Why Choose a Reliable Manufacturer
Choosing a trustworthy blow molding machine manufacturer is critical for ensuring the quality and efficiency of production processes. The right manufacturer will not only provide high-quality equipment but also support the long-term success of your operations.
Importance of Quality in Blow Molding Machines
Quality is paramount in blow molding machines because it determines the durability, efficiency, and output of the production process. A reliable machine will offer:
- Consistency: High-quality machines ensure that the production process yields uniform results, which is essential for maintaining product standards.
- Efficiency: A well-manufactured machine minimizes downtime, maximizing productivity and profitability.
- Cost-effectiveness: Investing in quality equipment may have a higher upfront cost, but it often results in lower operating costs and longer-term savings.
Assessing Manufacturer Reputation
When choosing a blow molding machine manufacturer, assess their reputation in the industry. Key factors to consider include:
- Industry Experience: Look for manufacturers with a long-standing presence and experience in the blow molding market.
- Customer Reviews: Investigate customer testimonials and case studies to gauge satisfaction and reliability.
- Certifications: Ensure that the manufacturer adheres to industry standards, as indicated by certifications like ISO or CE.
Cost vs. Quality Comparison
Budgets are always a concern in manufacturing; however, prioritizing quality over the lowest price can lead to better long-term investments. Cost analysis should consider:
- Lifecycle Costs: Evaluate not just the purchase price but also energy efficiency, maintenance needs, and potential downtime costs.
- Support Services: Quality manufacturers often provide comprehensive after-sales support, including maintenance and training, which saves costs in the long run.
Leading Blow Molding Machine Manufacturers
The blow molding industry hosts a variety of manufacturers known for advancing technology and providing durable machinery. Identifying key players can help in selecting the right equipment.
Top Players in the Industry
Some of the most recognized names in blow molding machinery include:
- Uniloy: Renowned for its innovative technologies and offering diverse solutions including blow molds.
- Wilmington Machinery: A leader in high-speed rotary extrusion machines, noted for superior technology in monolayer and multilayer systems.
- Jomar Corporation: Known for its injection blow molding machines and their industry experience spanning over 50 years.
- Bekum: Offers a portfolio of successful blow-moulding machines in America, focusing on high efficiency and low footprint design.
- Graham Engineering: Known for its advanced machinery that integrates modern features for efficiency and productivity.
Key Features to Look For
When assessing manufacturers and their machines, certain features should be prioritized:
- Automation: Advanced blow molding machines offer automation for streamlined operations.
- Energy Efficiency: Look for machines designed to reduce energy consumption and minimize operating costs.
- Flexibility: Machines that can adapt to producing different sizes and types of products can benefit diverse operations.
- Safety Features: Innovative safety measures such as emergency stops and guards to protect operators are essential.
Case Studies of Successful Implementations
Examining practical implementations can provide insights into the operational efficiency and effectiveness of particular machines. Successful implementations often illustrate:
- Increased Production Rates: A case where a company upgraded its blow molding machines resulting in 25% faster production times.
- Cost Savings: An example of a manufacturer reducing operating costs by integrating energy-efficient blow molding technology.
- Quality Improvements: A user case showcasing how improved machinery led to a 30% decrease in defects in the final product.
Advancements in Blow Molding Technology
The realm of blow molding is continually evolving as new technologies emerge. Staying abreast of these advancements is crucial for operators looking to optimize their processes.
Innovative Features in Modern Machines
Modern blow molding machines come equipped with features that enhance productivity and product quality. Notable innovations include:
- Smart Technology: Integration of IoT allows for real-time monitoring of machine performance, leading to proactive maintenance.
- Enhanced Controls: Advanced control systems facilitate precision in production, enabling the manufacturing of complex designs.
- Modular Designs: Facilities can upgrade or expand capabilities without needing to replace entire systems by utilizing modular systems.
Integration with Industry 4.0
The rise of Industry 4.0 has revolutionized blow molding processes through digitization and data utilization. Key aspects include:
- Data Analytics: Utilizing data gathered from machine performance to optimize production schedules and reduce waste.
- Predictive Maintenance: Employing machine learning algorithms to predict failures before they occur, minimizing downtime.
Efficiency and Sustainability Trends
As global sustainability efforts increase, blow molding manufacturers are focusing on reducing their environmental impact. Current trends include:
- Recyclable Materials: Increasing use of recyclable materials in production can lead to a smaller ecological footprint.
- Energy-efficient Processes: Development of machines that require less energy and produce less waste during the manufacturing phase.
Choosing the Right Blow Molding Machine
Deciding on the right blow molding machinery is a complex process influenced by various factors. A thorough evaluation can lead to significant operational improvements.
Factors to Consider When Purchasing
Consider the following key factors when researching and selecting a blow molding machine:
- Production Volume Needs: Assess the anticipated volume to ensure the machine will meet production demands.
- Material Compatibility: Ensure that the machine can handle the types of plastics you intend to use.
- Space Considerations: Evaluate the physical layout of your production facility and ensure there is adequate space for the machine.
Maintenance and Support Services
The provision of maintenance and support services is crucial to the longevity and effectiveness of any machinery. Look for:
- Warranty Terms: A strong warranty can protect against unexpected failures.
- Availability of Spare Parts: Ensure that spare parts are readily available to minimize downtime due to maintenance requirements.
- Technical Support: Reliable manufacturers often provide robust tech support to assist with any operational issues that arise.
Future-Proofing Your Investment
As technology advances rapidly, making informed decisions now can safeguard against obsolescence. Consider future-proofing strategies such as:
- Scalability: Select machines that can adapt to changing production needs without needing complete replacement.
- Technology Upgrades: Opt for systems that allow for easy upgrades of software and hardware components.